Robots in metalworking/processing
RoboSaw robotic sawing line
RoboSaw robotic sawing line
In the metalworking industry today, most manufacturing processes are apparently carried out by machine or automated. At second glance, however, it becomes clear that in most cases these are hybrid systems consisting of man and machine or partial automation.
Small batch sizes in metal processing make automation difficult
In a sawing center, a large number of orders have to be processed within short delivery times and usually with very small batch sizes (often they are one-offs) with a wide range of materials and the most varied cutting sizes. Full automation therefore did not seem feasible until now, since too many steps required human intervention and new individual solutions always had to be found. However, the Augsburg-based automation specialist AROTEC Automation und Robotik demonstrates with its RoboSaw robot-assisted sawing line that it is possible to carry out the manufacturing process almost entirely by machine, despite very small batch sizes.
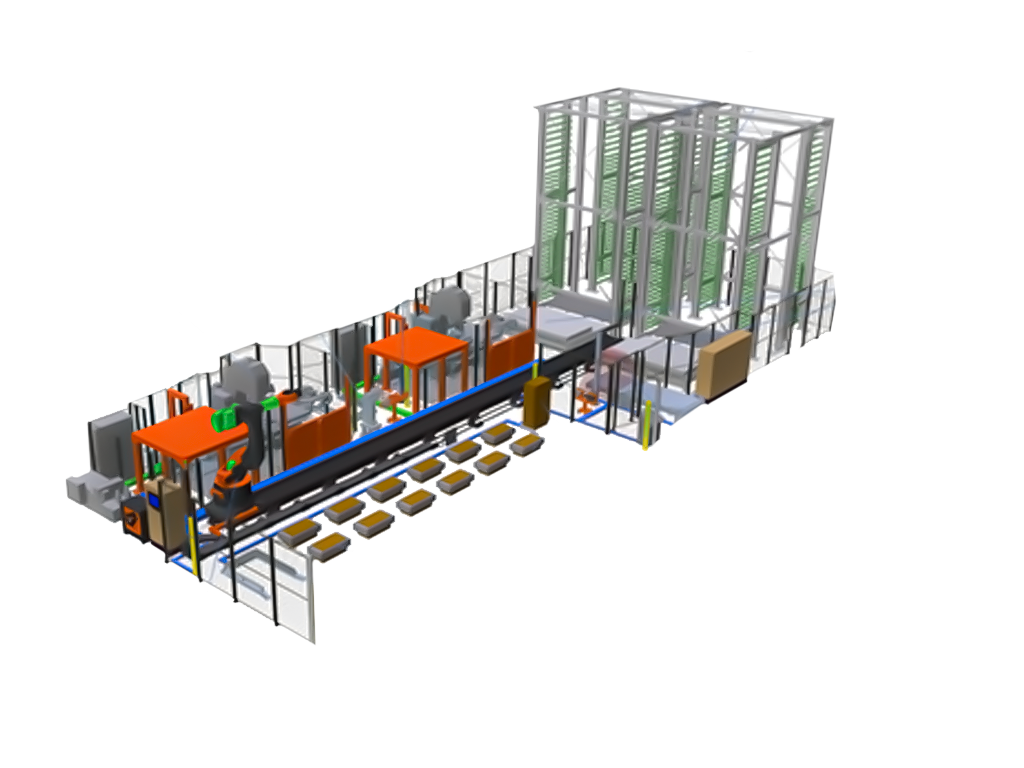
Storage tower
Stock pallet
Stock pallet
Conveyor/storage belt
3D measurement
Empty pallet stack
Alignment/Removal Station
Deburring/Brushing Station
Finished pallets
Robot with end effector
Vertical band saw
AROTEC shows a solution
The raw material, any materials and material sizes, are fed to the sawing line via a conveyor belt. The material is detected by a 3D vision sensor and measured with millimeter precision. Thereupon, with the help of the integrated palletizing algorithm developed by AROTEC PALGO@Mix a suitable storage location within the material warehouse (with 110 storage pallets) is selected. The storage and retrieval of material then takes place fully automatically and can take place in parallel to the cut processing of the RoboSaw.
The customer's ERP transfers the customer orders directly into the database of the RoboSaw's plant control computer. The order data contains, among other things, information about the customer, the agreed delivery date, the cutting dimension, the material quality and the respective quantity.
The line control computer determines the sequence in which the jobs are processed, taking into account the lowest possible waste and other criteria. The entire subsequent sequence of steps is initiated by the line control computer. From the procurement of material from the warehouse to the setting of the saw cut to the storage of the remaining material, the processing is fully automated.
If an order cannot be processed with the current material stock, this is immediately displayed to the order planner and the plant operator on the web-based plant visualization. The order planner can then take action and adjust the material stock. In addition, the prioritization of the orders can be changed. The comparison between the order sequence and the delivery dates takes place automatically on a regular basis and includes parameters such as a changed stock level or a manually set prioritization in the optimization of the order sequence.
The fully automated sawing line developed and implemented by AROTEC is unparalleled worldwide and is a prime example in the age of Industry 4.0. The sawing line demonstrates what is technically possible today and what potential can be exploited in the field of metalworking, especially in high-wage countries like Germany.
We would be happy to provide you with more information about the RoboSaw robot system. Please contact us here.
Robot-assisted sawing line - AROTEC Automation und Robotik GmbH
Talk to us now about robot-assisted automation of your production processes.
We also develop a customized robot system for you. No matter how complicated your requirements may be. No matter in which industry you are active.